INTRODUCTION:
Garment fitting is based on taking body measurements. So it is very important for a dress maker to know how to take accurate measurements. The following points will be very useful, for this purpose.
Garment fitting is based on taking body measurements. So it is very important for a dress maker to know how to take accurate measurements. The following points will be very useful, for this purpose.
BODY MEASUREMENT:
a. Care to be taken:
1. Try to know the customer’s requirements, regarding the fit, style and shape of the garment (pockets, collar, buttons, seam, finish etc.) before taking measurements. A preliminary talk with the customer, showing fashion pictures are stitched garment will help one to understand the design.
1. Try to know the customer’s requirements, regarding the fit, style and shape of the garment (pockets, collar, buttons, seam, finish etc.) before taking measurements. A preliminary talk with the customer, showing fashion pictures are stitched garment will help one to understand the design.
2. Observe the figure carefully and if any deviation in proportion is found, do not simply remember but record it in the order book, in without giving any idea of the deformity to the customer.
3. The person to be measured should stand erect, but in a natural pose, in front of a mirror.
4. Measurements should be taken comfortably without pulling the tape too tight or loose.
5. The measurements should be taken in proper order and with a certain sequence.
6. All girth measures should be taken tightly, as ease for movement is included in the draft.
7. To avoid any mistake, take the measurements twice.
b. Observing Human Body:For a successful garment cutting, one must know the size and shape of the human body, for which he has to design. A student should therefore remember the following points about the anatomy, before he starts to learn cutting.
Eight Head Theory:
A grown up human body is divided into eight equal parts, which are equal in height to that of the head. So each part is known as the “head”. All these eight divisions or heads are as follows :
A grown up human body is divided into eight equal parts, which are equal in height to that of the head. So each part is known as the “head”. All these eight divisions or heads are as follows :
1st head : From hair to chin or nape of neck.
2nd head : From chin to chest or bottom of scye.
3rd head : From bottom of armhole to waist.
4th head : From waist to hip.

5th head : From hip to mid thigh
6th head : From mid-thigh to below knee
7th head : From knee to calf muscle
8th head : From calf to tip of toe.
b. Calculating other measurements using chest circumference:
Measurements Men Women
Waist Chest – (4 to 5”) Chest – (5” to 7”)
Hip Chest + (1 to 2”) Chest + (2 to 4”)
Shoulder (Half) ¼ Chest – ½” 1/6 Chest + (1 to 2”)
Armscye depth 1/8 Chest + 1” 1/8 Chest + (2” to 2.5”)
Neck 1/3 Chest + (2 to 3”) 1/3 Chest + (2 to 2½”)
Hip Chest + (1 to 2”) Chest + (2 to 4”)
Shoulder (Half) ¼ Chest – ½” 1/6 Chest + (1 to 2”)
Armscye depth 1/8 Chest + 1” 1/8 Chest + (2” to 2.5”)
Neck 1/3 Chest + (2 to 3”) 1/3 Chest + (2 to 2½”)
TAKING BODY MEASUREMENT:
a. Bodice measurement:
1. Bust:
Measure around the fullest part of the bust raising the measuring tape slightly to a level just below the shoulder blades at the back.
Measure around the fullest part of the bust raising the measuring tape slightly to a level just below the shoulder blades at the back.
2. Waist:
Measure snugly around the waist keeping the tape parallel to the floor.
Measure snugly around the waist keeping the tape parallel to the floor.
3. Neck:
Measure around the the neck, passing the tape just above the collar bone time front and along the base of the neck at the back.
Measure around the the neck, passing the tape just above the collar bone time front and along the base of the neck at the back.
4. Shoulder:
Measure from the neck joint to the arm joint along the middle of the shoulder (A to B in fig. a)
Measure from the neck joint to the arm joint along the middle of the shoulder (A to B in fig. a)
5. Front waist length:
Measure down from highest point of shoulder to waist line through the fullest part of the bust (A to C fig. a)
Measure down from highest point of shoulder to waist line through the fullest part of the bust (A to C fig. a)
6. Shoulder to bust:
Measure down from highest point of shoulder to tip of bust (A to D in fig. a)
Measure down from highest point of shoulder to tip of bust (A to D in fig. a)
7. Distance between bust points:
Measure in the horizontal direction, the distance between the two bust points (D to E fig. a)
Measure in the horizontal direction, the distance between the two bust points (D to E fig. a)
8. Back width or across back measurement:
Measure across back from armhole to armhole about 3 inches below base of neck (P to Q in fig b)
Measure across back from armhole to armhole about 3 inches below base of neck (P to Q in fig b)
9. Back waist length:
Measure from the base of neck at the centre back to waist line (R to S in Fig b).
Measure from the base of neck at the centre back to waist line (R to S in Fig b).
10. Armscye depth:
Measure from base of neck at centre back to a point directly below it and in level with the bottom of the arm where it joins the body. (R to T in fig b).
Measure from base of neck at centre back to a point directly below it and in level with the bottom of the arm where it joins the body. (R to T in fig b).
c. Sleeve measurements:
11. Upper arm circumference:
Measure around the fullest part of the arm.
Measure around the fullest part of the arm.
12. Lower arm:
For lower arm, measure around the arm at desired level corresponding to lower edge of sleeve.
For lower arm, measure around the arm at desired level corresponding to lower edge of sleeve.
13. Elbow circumference:
Measure around the arm at elbow.
Measure around the arm at elbow.
14. Wrist:
Measure around the wrist.
Measure around the wrist.
15. Sleeve Length:
For short sleeve length, measure down from tip of shoulder at top of arm to desired length of sleeve (B to F in a) For elbow length sleeve measure from top arm to elbow point (B to G in a) For full length bend the elbow slightly and measure down from to of arm to back of wrist passing the tape over the elbow point (B to H in a).
d. Skirt measurements:
Waist:
Measure snugly around the waist keeping the tape parallel to the floor.
For short sleeve length, measure down from tip of shoulder at top of arm to desired length of sleeve (B to F in a) For elbow length sleeve measure from top arm to elbow point (B to G in a) For full length bend the elbow slightly and measure down from to of arm to back of wrist passing the tape over the elbow point (B to H in a).

Waist:
Measure snugly around the waist keeping the tape parallel to the floor.
16. Hip:
Measure around the fullest part of the hip horizontally. (7” to 9” from waist approx.)
Measure around the fullest part of the hip horizontally. (7” to 9” from waist approx.)
17. Waist to Hip:
Measure down from waist at centre back to fullest part of the hip (S to U in fig.b).
Measure down from waist at centre back to fullest part of the hip (S to U in fig.b).
18. Skirt Length:
Measure down the centre back from waist to desired length of skirt (S to V in fig. b) length from waist to floor can be taken at the same time and te difference between the two noted. This difference will give the number of inches the skirt is above the floor level. After taking your measurements compare then with the sample measurements for ladies garments given table. 1. Any measurement which appears too small or exaggerated must be rechecked at once.
Measure down the centre back from waist to desired length of skirt (S to V in fig. b) length from waist to floor can be taken at the same time and te difference between the two noted. This difference will give the number of inches the skirt is above the floor level. After taking your measurements compare then with the sample measurements for ladies garments given table. 1. Any measurement which appears too small or exaggerated must be rechecked at once.
Sample measurements for ladies garments
(All measurements are inches)
(All measurements are inches)
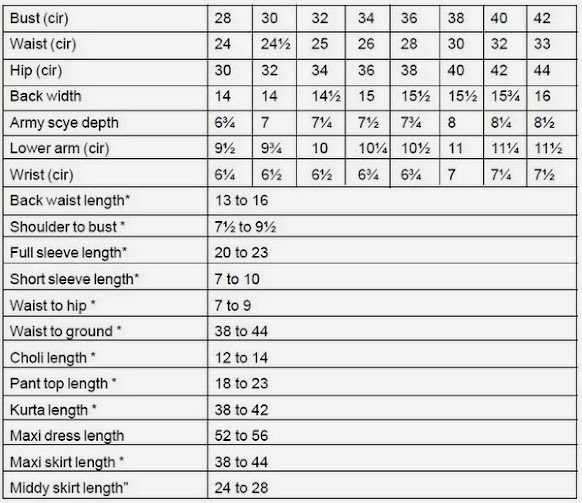
Sample measurments for childern’s garments
(All measurements are in inches)
(All measurements are in inches)

(i.e. all except the last four items in the table) apply also to boys.
Sample measurements for boys’ garments
(All measurements are in inches)
(All measurements are in inches)
